Simulated Process Improvement is Easy!
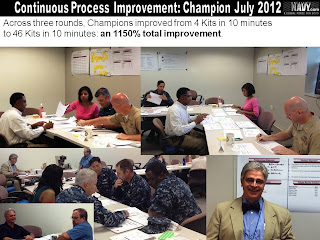
We just completed the first annual training cycle (Oct 2012-Sept 2012) of our resurrected Continuous Process Improvement program. Our first year goals (and invested resources) were fairly modest. We planned to train an initial cadre of practitioners (check), execute several proof-of-concept projects (check), re-institute the local CPI collaborative (check), grow an in-house instructional capability (check), and embed CPI as an integral part of the strategic planning process (semi-check). In some ways, I think we might have aimed too low. It is common to achieve 1000% improvements in simulated processes during training. In our most recent class, we improved over a baseline production of 4 products in 10 minutes to a final production of 46 products in 10 minutes -- 1150% improvement in production and a cycle time improvement from 150 seconds per product down to about 13 seconds per product. If we could accomplish that in real life -- our biggest problem would be trying to figure out ho