Today and Tomorrow: Commemorative Edition of Ford's 1926 Classic by Henry Ford My rating: 4 of 5 stars Brilliant, though somewhat utopian in outlook. I was somewhat surprised to see that Henry Ford outlined a complete and modern continuous process improvement program back in 1926 -- long before quality circles, total quality management, and lean six sigma. The basic message of the book is that good business management can save the world. Ford cites multiple examples from Ford Motors where better management improved the bottom line and also improved the lives of his workers. The book reads somewhat like an Ayn Rand novel - the producers of the world carry the load for the moochers. Ford does offer ample advice and has a very quotable writing style. The only thing that kept me from giving it five stars was the constant droning about how Ford Motors is the best thing since sliced bread. Otherwise, this is a very good book, maybe a must read, for those interested in continuou
Posts
Simulated Process Improvement is Easy!
- Get link
- Other Apps
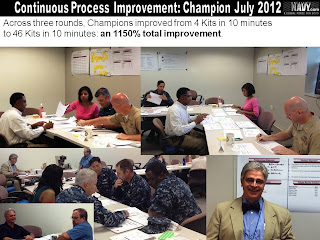
We just completed the first annual training cycle (Oct 2012-Sept 2012) of our resurrected Continuous Process Improvement program. Our first year goals (and invested resources) were fairly modest. We planned to train an initial cadre of practitioners (check), execute several proof-of-concept projects (check), re-institute the local CPI collaborative (check), grow an in-house instructional capability (check), and embed CPI as an integral part of the strategic planning process (semi-check). In some ways, I think we might have aimed too low. It is common to achieve 1000% improvements in simulated processes during training. In our most recent class, we improved over a baseline production of 4 products in 10 minutes to a final production of 46 products in 10 minutes -- 1150% improvement in production and a cycle time improvement from 150 seconds per product down to about 13 seconds per product. If we could accomplish that in real life -- our biggest problem would be trying to figure out ho
Acknowledging Milestones: 50 Projects and Counting
- Get link
- Other Apps
Two overlapping tidbits of information caught my eye this last week. First, I am trying to persuade my boss to send me to a Lean Six Sigma Master Black Belt course. In the description of the course, a Master Black Belt candidate is described as a Black Belt with an experience level equivalent to 50 process improvement projects. Second, I visited the blog of a very well-known practitioner who indicates that his experience level consists of "over 250 projects" completed. It got me thinking: I wonder how many projects I have completed? I found it surprisingly hard to count projects, even harder to count them honestly. The hard part isn't remembering the work. The hard part is determining what constitutes a project, and which projects count as personal experience. Do all projects have to be continuous process improvement to count? Does a rapid improvement event count as a project, or should I only count full projects? If I manage the project manager (i.e., he or she works
The Paradox of the Low Hanging Fruit
- Get link
- Other Apps
In business projects, the metaphorical language of picking the low-hanging fruit almost always comes up. Just to be clear, the low-hanging fruit refers to the idea that the easiest or lowest cost work should get done first. Examples of low-hanging fruit include things like eliminating obvious waste, cutting overtime, reducing excessive stockpiles, and removing self-inflicted policy constraints. Good things generally happen when you pick the low-hanging fruit. First, the project team can satisfy an immediate need to be successful, if only on a small scale. Because the low-hanging fruit is so easy to get, harvesting it early in a project can generate momentum for a more sustained effort. Second, everyone on the team can agree. Because the low-hanging fruit is obvious, disagreements on the obvious course of action are normally quite easy to resolve. Third, the project team can de-clutter the solution space. Getting the little things out of the way can help the team stay focused on the
Lubricating the Social Machinery: Tips for Using Humor in Public Speaking - Yahoo! Voices - voices.yahoo.com
- Get link
- Other Apps
Garden Synchronicity: Defective Cucumbers and Resistance to Change
- Get link
- Other Apps
I started a garden for the first time last year (2011). I wasn't very good at it, but I learned a lot about what to do and what not to do. I learned that planting flowers with the vegetables helps attract beneficial insects. I learned that too much water can be just as bad as not enough. I also learned that plants grow better when organic material (a.k.a. compost) is tilled into the soil. So at the end of last year, I put all of the garden and yard waste in a compost bin. Rotten tomatoes, corn stalks, grass clippings, fallen leaves, and dried sunflower plants all went into the bin. When spring came, I dumped out the compost bin and used a roto-tiller to mix it all into the garden patch. As a process improvement over last year's garden, I actually had a plan for Garden 2012. I knew that I didn't want any more sunflowers, because they blocked out the sun for other plants. I knew that I wanted cucumbers, so I bought premium seeds and planted them in the northeast corner o
Intangible Value in Small Projects
- Get link
- Other Apps
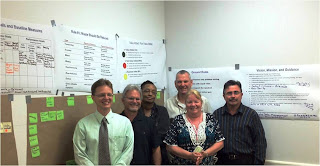
How big does a continuous process improvement project need to be? I get variations of this question every time I provide training on the topic. My best answer goes something like this: "The tools and techniques of CPI are scalable to accommodate both large and small projects. Black belt projects are normally larger and more complex than green belt and yellow belt projects. In a typical cross-functional process map with four departments and 30 steps, a yellow belt might do a project on one step, a green belt might do a project on one department, and a black belt might do a project on the entire process." Two hidden issues underlie this question. Issue number one is that people believe that every project must provide substantial and tangible benefits to be worthwhile; they believe that doing small projects is a waste of time. The truth is that there is value in doing a CPI project, however small, for the sake of doing the project. Colleagues might argue that projects consu